It CAN change, it will just take a little longer
- SiteWorks Mechanical
- Apr 6, 2020
- 3 min read
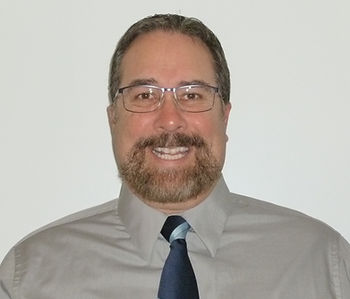
Happy Tuesday everybody and I hope that you are all well. One of the people that I follow is Dr. Klaus M. Blache. He is someone that I consider a mentor because of what I have learned from him over the years. He is based in Knoxville and he is director of the Reliability & Maintainability Center at the Univ. of Tennessee, and a research professor in the College of Engineering. So, I do consider him an expert.
I want to pass on a question asked that he answered in a past issue of Efficient Plant.
Q: Is your maintenance process beyond the tipping point?
A: To answer this, it’s important to understand the concept of “tipping point.” When the tipping point of a system is crossed, negative and mostly unpredictable consequences occur in your process. An undesired practice (more typically many harmful practices) is responsible for pushing the system beyond the point of no return, i.e., corrections are no longer possible with known solutions. Furthermore, these negative effects start to happen more frequently and with more-significant negative outcomes until the process collapses.
I know myself that I have seen this tipping point firsthand and many of you reading this have seen it also. This discussion on tipping points happens regularly about climate change. Climate scientists and the National Oceanic and Atmospheric Administration flagged 400 to 450 ppm CO2 (the primary greenhouse gas) as the point of no return. This means that the balance of the interconnected and interdependent processes that make up our ecosystems may no longer be correctable, based on what is known today.
Your reliability and maintenance (R&M) process also has tipping points and, if you’re watching, there are indicators that those points are about to be reached. Examples are the level of reactive maintenance performed, PM compliance, maintenance-work-order backup, and activity involving planning and kitting maintenance tasks. Once you cross enough of those tipping points, your R&M process is out of control.
For example, if reactive maintenance is high, you will never have enough spare parts. One poor practice leads to a negative outcome. Since all facets of a system are related, when poor practices increase, negative consequences compound and grow at an increasing rate to a point of no return. The result is catastrophic.
The dynamic systems and processes of the Earth are fairly resilient but can only self-correct to a point. Similarly, your reliability and maintenance process is a living system that can self-improve through workforce efforts. Individuals are using more technology, working on parts rationalization, and performing PM optimization. Many are realizing some localized benefits.
If too many related daily practices are over their tipping point, however, you are at a point where it’s difficult, if not impossible, to make a meaningful (sustainable) improvement without major and all-inclusive changes. How can you properly maintain and respond to production equipment needs if your backlog is out of control? How can you be assured that parts will be available, without excessive overstocking, and/or if parts usage and restocking is not accurately linked in your CMMS (computerized maintenance management system)? Are all of your jobs entered into your CMMS or do you respond to verbal requests? How do you control, plan, and forecast for anything if you don’t trust your data? If you don’t improve culture, how do you expect to get to top-quartile performance?
Realistically assess your current state to decide if your process is fixable with some continuous improvement or requires a total rework. Fortunately, in R&M you can start over and fix the system and processes.
This W. Edward Deming quote sums it up, “It is not necessary to change. Survival is not mandatory.” If your sky is falling, don’t wait for someone else to fix it. They may not come. Some of the best improvements in R&M processes that I have seen were started and implemented by an individual or small team that followed their vision with tenacity. Doing nothing is a decision and probably not the correct one.
One thing that we are about to realize is that after this Covid-19 shutdown, many pieces of equipment and machinery will not come back to life. They will find out how by not practicing a proactive maintenance and becoming purely reactive all those small chronic issues that were not addressed because of reactive maintenance will actually become your million-dollar problems.
Comments